WE PRESENT YOU SOME OF OUR LARGEST PROJECTS BELOW
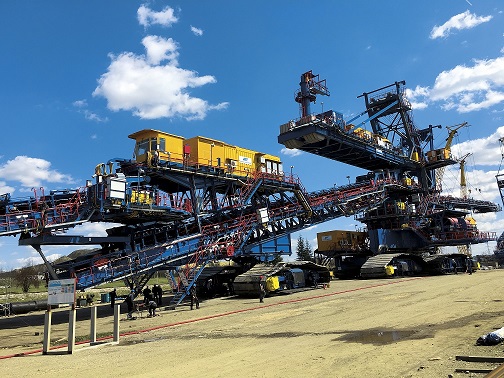
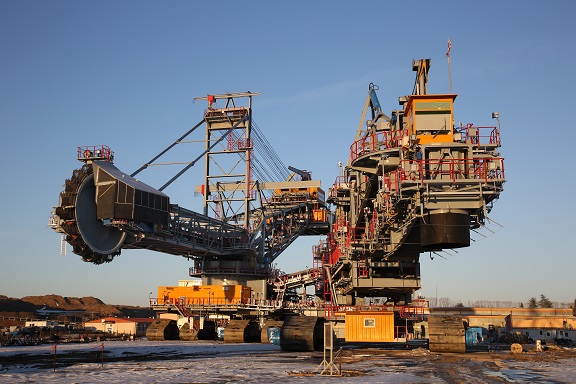
Mikro Kontrol delivered complete electrical system for a Portal Bridge Stacker for gold sludge in Hydrometallurgical Plant 3 (GMZ-3) of the Navoi Mining and Metallurgical Plant, Uzbekistan.
Scope of Work
Mikro Kontrol provided detailed and as-built design, electrical equipment assembling and delivery, installation materials delivery, site supervision, test and commissioning.
Benefits
- Turn-Key solution
- State-of-the-art equipment
- Advanced drive and software solutions against bridge misalignment
- Maximum level of reliability and availability
- Operation and maintenance convenience
Technical Description
The main power supply 380V, 50Hz is realized over festoon system. The power supply for movable spreader conveyor and its travel drives are realized as sub-distribution over festoon system as well. The main MCC and PLC are located on the bridge itself.
Bridge Drives and Spreader Conveyor Travel Drives are designed as Variable Frequency Drives. The bridge drives are operating synchronously in load-sharing master-slave operating mode. There is a multi-turn absolute encoder to measure travel and a reference marker on the both sides of the bridge.
PLC software is tracking parameters and making corrections against Bridge misalignment. Operator desk with HMI touch panel, operator joysticks and signaling and control elements is in operator room next to the stockyard. Communication between control elements is realized over Profinet communication.
All the used components and materials are designed for harsh environment and operation in mine.We successfully accomplished over 45 automation projects in metals.
WE PRESENT YOU SOME OF OUR LARGEST PROJECTS BELOW
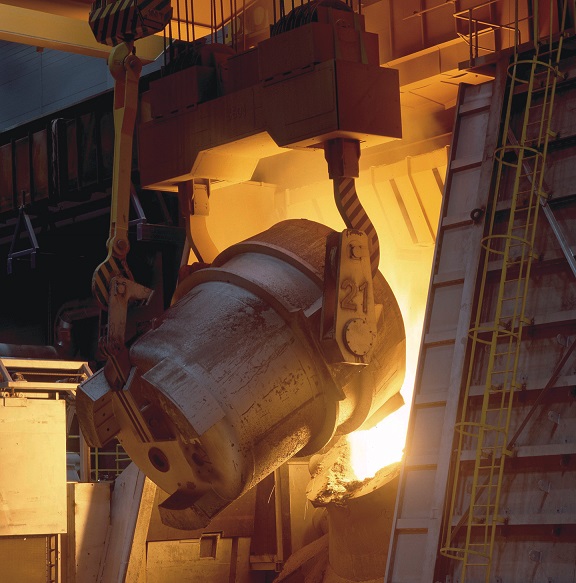
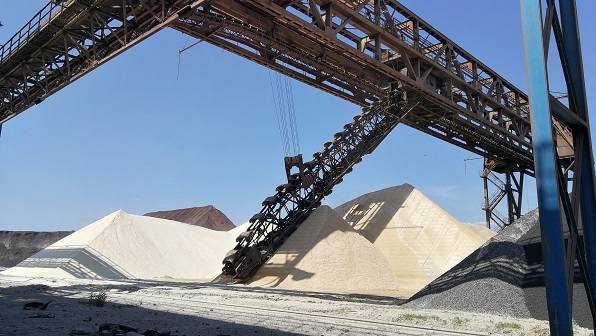
- State-of-the Art equipment and solution; the old machine was out of work for several years
- Increasing production capacity and product quality
- Maximum level of reliability and availability
- Operation and maintenance convenience
- The whole project is done within 6 months. It’s successful realization encourages customer to plan the modernization of the second casting machine.
We successfully accomplished over 65 automation projects in power.
WE PRESENT YOU SOME OF OUR LARGEST PROJECTS BELOW
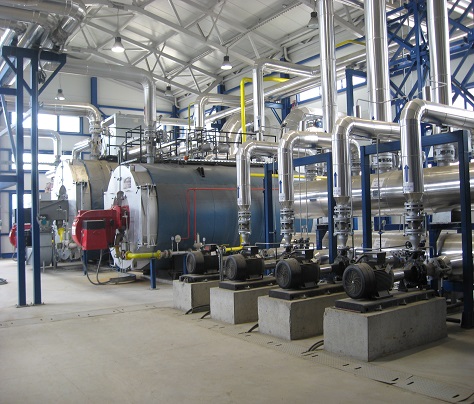
- Maximum level of reliability and availability
- Very fast system errors detection
- Easy and efficient maintenance
-
Pressure and temperature
-
Flue gas oxygen ratio (O2)
-
Water flow at return pipeline
We successfully accomplished over 35 automation projects in chemical and pharma industry.
WE PRESENT YOU SOME OF OUR LARGEST PROJECTS BELOW
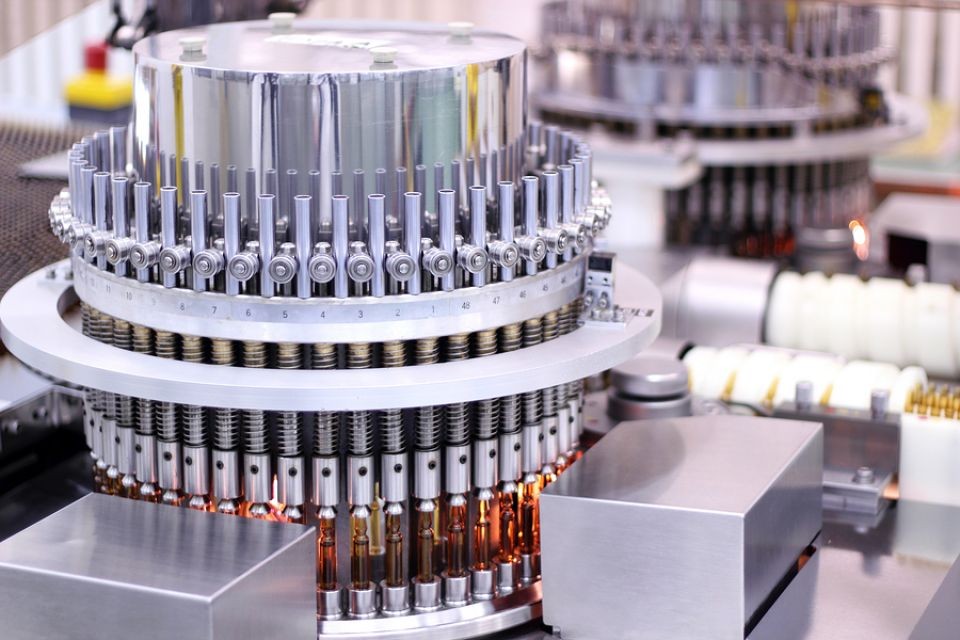
- Increase of production capacity
- improved safety
- better end-product quality
- maximum level of reliability and availability
- operation and maintenance convenience
- lower maintenance costs
We successfully accomplished over 60 automation projects in water and environmental.
WE PRESENT YOU SOME OF OUR LARGEST PROJECTS BELOW
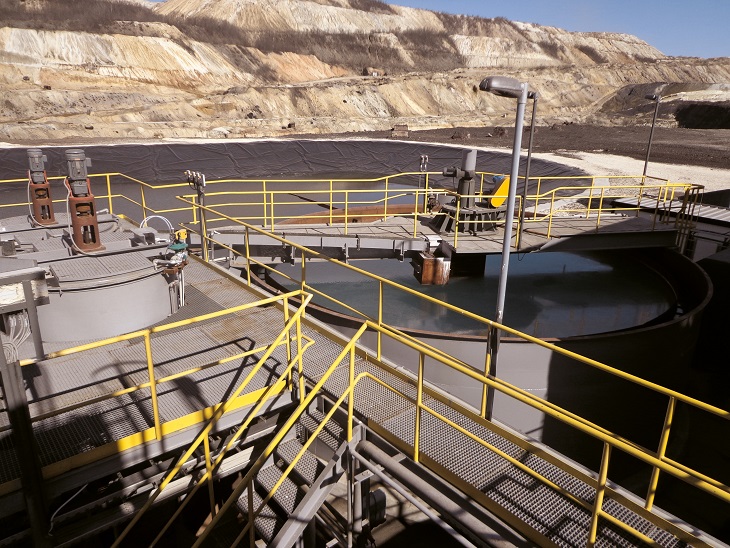
The Japanese government approved the donation to upgrade the supervisory control and data acquisition system (SCADA) for the Belgrade Water Supply System.
The scope of the project was to establish a SCADA system for control and monitoring of all wells, distribution pumping stations and reservoirs, reconstruction of the 7 main distributive pump stations and renewal of the equipment for water quality analysis.
Scope of Work
Mikro Kontrol provided detailed and As-built electrical designs, delivery and installation of the whole equipment, PLC and HMI software programming, electrical mounting on all sites, as well as commissioning.
The delivered equipment included:
- 14 server racks with belonging SCADA workstations
- 126 new PLCs as well as around 80 existing on which applicative adaptations were made in order to connect them to the system
- 25 touch operator panels
- 20 chlorine analyzers
- 26 L3 switches, 32 SHDSL routers and 149 GPRS routers
Benefits
- Maximum level of reliability and availability
- Increased energy efficiency
- State-of-the-art equipment and solution
- Operation and maintenance convenience
Technical Description
SCADA system covered 155 totally location:
- MCC - Main Control Center at 1 location
- LCC - Local Control Center at 4 locations
- Pumping stations of type A (with a local SCADA server) 14 locations
- Pumping stations of type B (without a local SCADA server) 14 locations
- Wells at 102 locations
- Reservoirs at 20 locations
The main functional tasks placed in front of the SCADA system included data acquisition, monitoring and real-time data archiving from all facilities connected to the system (around 10.000 tags), real-time control and monitoring of 102 wells and 7 main pump stations, as well as the real-time monitoring of all distributive pumping stations and reservoirs.
We successfully accomplished over 120 automation projects in food industry.
WE PRESENT YOU SOME OF OUR LARGEST PROJECTS BELOW
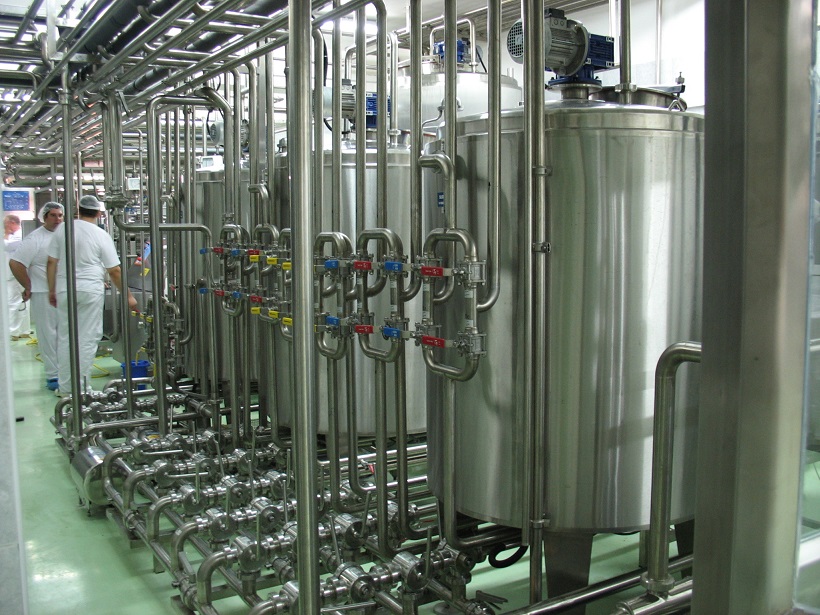
- Fully CIP automated process
- Maximum level of reliability and availability
- Operation and maintenance convenience
Automatic mode involves the implementation of the production process defined by the parameters of the selected procedure.
WE PRESENT YOU SOME OF OUR LARGEST PROJECTS BELOW
Mikro Kontrol developed a complete algorithm for control software based on function blocks, application software for safety controller, motion controller and HMI interface, and commissioning with performance test.
Benefits
- Very reliable, fast and modern control system based on the last generation Omron NJ Motion controller platform
- Safety protection integrated in safety controller and motion controller
- Parallel work of transport cars, controlled by the Omron servo drives, contributing to a very large line capacity
- Complete monitoring and parameter setting of the machine
- Established fast and efficient communication between all parts of production line
Technical Description
Standard parts of napkin production line include: paper unwinder, printing section, emboser section, longitudinal cutting and perforation, counting and packaging head, transporting part and part for transporting to the packaging machine.
To incerease the line capacity, Mikro Kontrol designed 4 production channels. On every channel, there are 2 pairs of transport cars, driven by 4 servo motors. Internal communication of transportation cars provide very fast and efficient transport without any possibility of collision and accidents.
In addition to many drives controlled by frequency converters, production line includes 24 servo axis capable of very quick and efficient task completion.
In order to avoid channel congestion and capacity decrease, the unloading part of the transport system intermittently moves packages from these 4 channels to an exit chanel on the packaging machine.
We successfully accomplished many automation projects in other industries such as Cranes, Rubber Industry, Mechatronics, HVAC ...
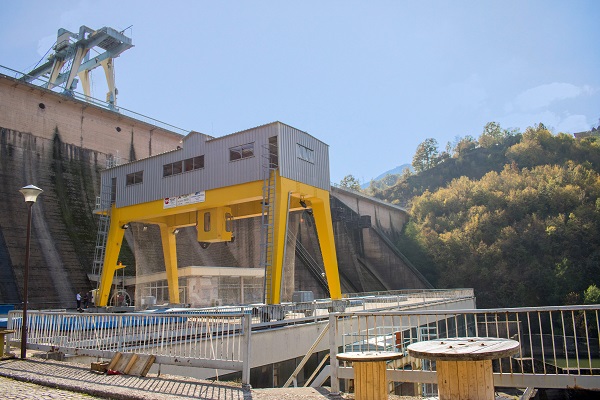
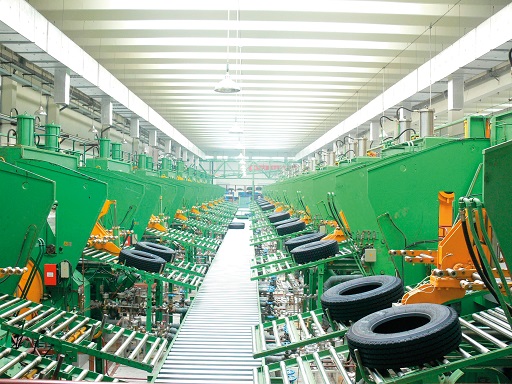
- Reliable work in both single and coupled mode
- No portal corruption
- The supervision and control of the load amount of each hook
- Safety circuit implemented
- Monitoring alarm system
- The speed limit in relation to the position and load management driving portal in terms of drive synchronization on both sides